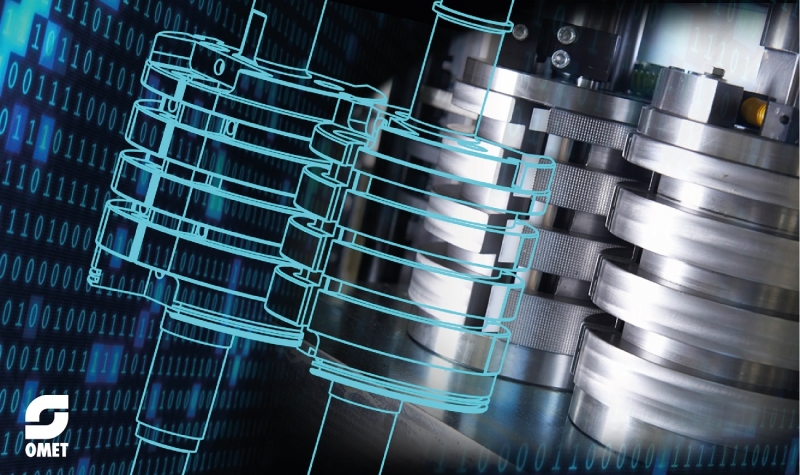
OMET 4.0 – NEXT STEP
Digital is increasingly present in OMET. After being one of the first manufacturers to offer a platform for collecting and managing the operating data of its lines, it takes a new step towards digitalisation with the introduction of the ‘Digital Twin’.
The digital twin is the virtual replica of a physical system, in this case a napkin production line. As machines become more complex, the way they are designed, tested and maintained must also evolve.
This concept is at the heart of virtual commissioning, which is a new way of testing the functionality and components of the machine even before it is built. This is how OMET’s engineers were able to overcome the current supply chain bottlenecks and achieve another important result: reducing the production time of the new XV line by 25%.
While the production departments are busy building and assembling the main components, the software engineers test the PLC and Motion Control programmes on the virtual copy of the machine. The Digital Twin brings with it all the physical characteristics of the real machine, and thanks to a development environment that also simulates conditions such as gravity, the validation process guarantees results that will be exactly replicated in reality.
By linking the digital model to the real machine software in the PLC, the internal logic of the line is tested, anticipating and reducing the debugging phases of the code; the simulation of the movements of the most complex systems makes it possible to avoid costly and dangerous collisions between moving axes.
Last but not least, working on a still ‘editable’ copy of the machine allows for greater collaboration between the mechanical and electronic departments, being able to make changes that facilitate the work of colleagues.
Virtual commissioning is only the first step towards the complete digitalisation of OMET’s plants. Researchers in R&D are already working on developing a digital copy of each machine, which will be constantly updated with the operating data of the real one, allowing predictive analyses to be carried out with a focus on continuous efficiency improvement.