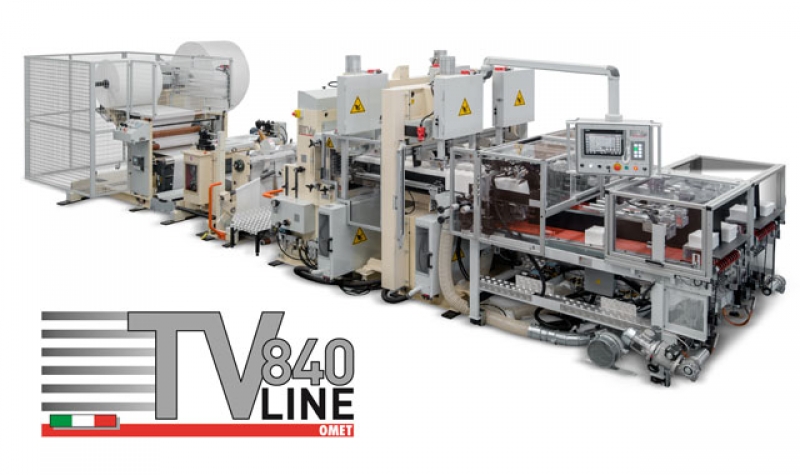
HIGH CAPACITY AUTOMATIC LINES FOR “TRIMMED” NAPKINS
by Alberto Redaelli
In the napkin converting scenario, most of the consumers around the world are accustomed to using ¼ fold or ⅛ fold napkins.
In fact, in the napkin market, these products have always been the most popular and widely used ones.
Curiously, in some markets, especially in Latin America, other types of napkins are still very popular, an important exception to this rule.
These types of napkins are known as “slitted” and “trimmed”.
Differently from the ¼ folded napkins, these products have either only two folds (“slitted” napkins) or just one individual sheet (“trimmed napkins”).
Whilst the size of the flat napkins is approximately the same as that of ¼ fold napkins, the open size is evidently very different: around half or quarter of the size of a conventional napkin.
The “slitted” and “trimmed” napkins are used equally for both household consumption and institutional market, representing a low-cost alternative to the regular and conventional napkin.
These napkins also require a different production process, as compared to the others, which involves a different conversion line set-up, a factor that can lead to some problems.
In the case of a vacuum folding line, the production of these napkins is more difficult than that of ¼ fold napkins because they are more lightweight. This reduces the stability of the sheets on the folding drums and the finishing operations also become more difficult, resulting in visibly irregular piling.
Furthermore, when the napkins are processed by an automatic folding machine, the conversion line requires a different cutting system from the one commonly used. This is a huge limitation that hinders the separation process and the automatic transfer to the packing system.
Today, these technical limitations are clearly lead to a substantial increase in the production costs of these products, due to the need for a larger workforce.
As part of an active development programme, the Omet R&D Team has successfully developed an innovative solution to this “bottleneck” problem in automatic processing.
The new line, developed from the successful TV 840 platform, has achieved all the project goals.
First, the napkin production has been transformed in a fully automatic process, from the reel to the finished product, delivering the desired quantity to the packing machine.
Second, an efficient cutting system, together with a precise automatic separation system, enables the production of more than 8,000 flat napkins and more than 15,000 pre-cut napkins per minute, requiring just one supervisor.
For all the TV 840 machines, the change of format is also extremely simple.
Furthermore, just 15 minutes are required to change product from “slitted” to “trimmed” napkin.
Third, the automatic transfer system is compatible with almost every type of automatic packing machine, so the automation process can even include box-packing and pallet systems.
Finally, this development provides further advantages in terms of showing the napkins in the finished package.
The package clip is perfectly aligned on all sides and package quality is excellent. This improvement in visual presentation provides extra added value to the product, making it stand out in the destination point-of-sale.
These innovative developments will certainly be a boost to this traditional and still widely used product, contributing at the same time by significantly decreasing the product’s cost of manufacture, as well as providing evident improvement in quality.
by Alberto Redaelli