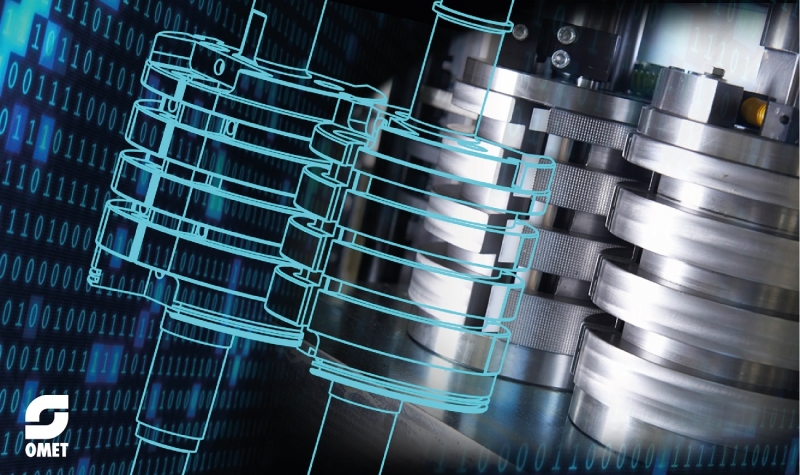
OMET 4.0 – NEXT STEP
Il digitale è sempre più presente nella realtà OMET. Dopo essere stata tra i primi costruttori ad offrire una piattaforma per la raccolta e la gestione dei dati di funzionamento delle proprie linee, compie un nuovo passo verso la digitalizzazione con l’introduzione del “Digital Twin”.
Il gemello digitale (“Digital Twin”) è la replica virtuale di un sistema fisico, in questo caso una linea per la produzione di tovaglioli. Man mano che le macchine diventano più complesse, anche il modo in cui vengono progettate, testate e mantenute deve evolvere.
Questo concetto è alla base del virtual commissioning, ovvero un nuovo modo per testare le funzionalità e i componenti della macchina ancora prima che questa venga costruita. E così che i tecnici OMET sono riusciti ad ovviare alle attuali criticità legate alla supply chain, ottenendo un altro importante risultato: ridurre del 25% i tempi di realizzazione della nuova linea XV.
Mentre i reparti produttivi sono impegnati nella costruzione e nel montaggio dei componenti principali, i softwaristi testano i programmi di PLC e Motion Control sulla copia virtuale della macchina. Il Digital Twin porta con se tutte le caratteristiche fisiche della macchina reale e grazie ad un ambiente di sviluppo che simula anche condizioni come la gravità, il processo di validazione garantisce risultati che verranno esattamente replicati nella realtà.
Collegando il modello digitale al software reale di macchina presente nel PLC, si testano le logiche interne della linea anticipando e riducendo le fasi di debug del codice; la simulazione dei movimenti dei sistemi più complessi permette di evitare costose e pericolose collisioni tra gli assi in movimento.
Non da ultimo, lavorare su una copia ancora “editabile” della macchina, consente una maggior collaborazione tra gli uffici meccanici ed elettronici, potendo apportare le modifiche che più facilitano il lavoro dei colleghi.
Il virtual commissioning è solo il primo passo verso la completa digitalizzazione degli impianti OMET. I ricercatori dell’R&D stanno già lavorando allo sviluppo di una copia digitale di ogni macchina, che verrà costantemente aggiornata con i dati di funzionamento di quella reale, consentendo di eseguire analisi predittive in un’ottica di miglioramento continuo dell’efficienza.