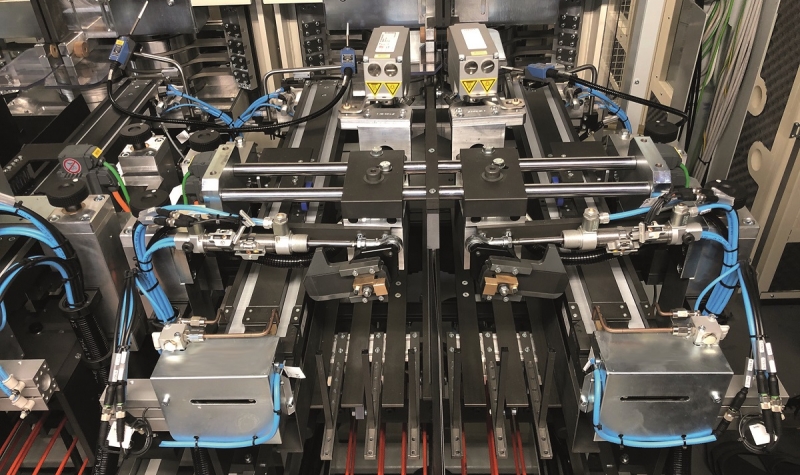
L’evoluzione verso il Service 4.0 non può prescindere dall’automazione delle strutture
L’industria 4.0 richiede collaborazioni interaziendali. OMET,produttore di macchine per il tissue converting, dimostra come rendere le linee di produzione adatte per il Service 4.0: ha sviluppato un software per il comando e la manutenzione a distanza dei suoi impianti. Prerequisito per la regolazione delle singole parti dell’impianto via HMI è il sistema di posizionamento di Lenord + Bauer, che aumenta la facilità d’uso e fornisce dati per la diagnosi dello stato.
Sistemi intelligenti e interconnessi digitalmente costituiscono la base dei concetti di Industria 4.0. L’interconnessione delle moderne tecnologie di informazione e comunicazione con concetti di controllo collaudati apre nuove possibilità per una produzione auto-organizzata. Si parla di sistemi auto-ottimizzanti. Non è ancora chiaro se alla fine agiranno in modo completamente autonomo o se, come sistemi di supporto, proporranno misure di ottimizzazione all’operatore. In ogni caso, dati e messaggi devono essere trasmessi in tempo reale all’organo decisionale. Devono inoltre poter essere eseguiti necessari interventi tecnici senza azioni manuali. La digitalizzazione spinge quindi l’uso automatizzato di macchine.
Il futuro sta nel valore aggiunto digitale
Anche OMET, leader di mercato delle macchine per il tissue converting, si affida a concetti di comando moderni ed efficienti. Service 4.0 è il nome della visione dello specialista italiano del tissue, che ha implementato nel suo Intelligent Plant Software. Il software italiano è orientato ai tool di supporto, in quanto rileva tendenze nei dati della macchina e le segnala a un punto di assistenza. L’analisi statistica dei dati consente di rilevare tempestivamente stati critici ripetitivi, aumentando così l’efficienza della linea di trasformazione grazie a interventi mirati. Sulla base delle tendenze dei dati il personale può identificare subito la causa di un allarme o di un avvertimento, tracciare il comportamento d’esercizio della macchina e, se necessario, adottare delle contromisure.
Con il concetto prodotto i³SAAC, Lenord, Bauer & Co. GmbH di Oberhausen segue un approccio analogo. Lo specialista di sensori di movimento e tecnologia di azionamento integrata fornisce prodotti che supportano applicazioni di Industria 4.0 a tre livelli. Il livello più basso è costituito dall’hardware. Dalla prospettiva della società di Oberhausen, attuatori e controller autonomi nonché sensori intelligenti e interattivi integrati sono necessari per realizzare sub-sistemi interconnessi digitalmente. Interfacce e servizi di comunicazione nonché tool per la messa in servizio e il controllo funzionale costituiscono a livello di integrazione il collegamento al mondo digitale. A livello di sistema, la società fornisce software e servizi digitali che facilitano l’attività di produttori di macchine e gestori. Entrambe le aziende sono aperte a tecnologie orientate al futuro che offrono ai loro clienti un valore aggiunto digitale.
Prerequisito: automazione!
Il funzionamento pratico è illustrato nell’esempio della linea di tissue converting di OMET, riportato di seguito. Per poter realizzare Service 4.0 anche nella linea di trasformazione TV840, la società ha dotato più macchine del sistema di posizionamento SeGMo completamente automatizzato di Lenord + Bauer. L’impianto trasforma giganteschi rotoli di carta per uso igienico in raffinati tovaglioli. In più fasi produce fino a 5.000 pezzi al minuto. La linea esegue tutte le fasi di lavorazione della catena di processo: a partire da srotolamento, stampa, impressione, arrotolamento, piegatura e taglio fino alla fardellatura. Finora l’unità di piegatura e formazione dei pacchetti a fine linea è stata comandata manualmente. Per consentire le attività di Service 4.0, attuatori compatti con coppie di 2,5 o 5 Nm unitamente a videocamere svolgono ora questo compito. In ogni linea sono installati in totale 12 SeGMo del tipo GEL 6109. A una unità di comando decentralizzata sono collegati rispettivamente quattro attuatori. Per il cablaggio ogni attuatore necessitava di un solo cavo ibrido pronto per il collegamento. La soluzione plug & play garantisce sia la comunicazione interna sia l’alimentazione di tensione tra scatola elettronica e attuatore. Ciascun attuatore è una unità meccatronica completa costituita da ingranaggio, micro controller, motore e sensore di posizione assoluto. Gli attuatori sono stati montati direttamente sul rispettivo asse tramite un albero cavo. Un supporto coppia impedisce all’attuatore di ruotare durante il funzionamento e funge da cuscinetto flottante compensando il gioco assiale dell’asse. Dopo l’installazione, il personale di montaggio in Italia ha controllato il funzionamento degli attuatori con il Support Tool del fornitore tedesco. Questo software lavora senza collegamento all’unità di controllo dell’impianto. Ogni singolo asse è stato impostato tramite il SeGMo-Box via interfaccia USB. Solo successivamente gli specialisti hanno collegato il sistema al Simatic S7-1516F di Siemens.
Risparmio di tempo non solo al riattrezzaggio
Gli esperti PLC di Lecco hanno utilizzato i blocchi funzionali Step 7 di Lenord + Bauer per integrare il sistema nell’S7. Questi template generano le autorizzazioni al movimento necessarie per comandare gli attuatori e trasmettere al PLC dati di stato quali corrente motore, posizione assoluta, temperatura apparecchio nonché valori di soglia. Ogni Box comunica con l’unità di controllo tramite interfaccia PROFINET, e inoltra i dati target agli attuatori. Ciascun attuatore regola in modo autonomo la velocità del rispettivo asse in base al comando di marcia. Il sistema di posizionamento forma una sottorete e alleggerisce la rete della macchina. Grazie alla gestione separata (alimentazione dedicata) di alimentazione motore e alimentazione dei circuiti logici nel cavo di collegamento degli attuatori, sia le funzioni di comunicazione che di diagnostica vengono mantenute anche quando l’alimentazione del motore è disinserita.
Le macchine per il tissue converting adesso possono essere impostate immettendo i parametri da terminale HMI, senza aprire la cabina di sicurezza. Grazie all’automazione della linea TV840 con il sistema SeGMo, il terminale di comando diventa un punto di controllo che consente facilita la gestione. La modifica della velocità o l’arresto e avvio si effettuano mediante la semplice pressione di un pulsante, così come la variazione delle dimensioni del prodotto, la piegatura nonché la relativa regolazione. In passato, ogni volta che veniva apportata una modifica, la produzione veniva interrotta dall’apertura dei dispositivi di sicurezza. Nel nuovo concetto di comando ciò non accade. Il personale operativo salva i valori d’impostazione in un sistema di gestione delle ricette. In questo modo si evitano errori di impostazione durante il funzionamento e si garantisce la massima precisione di ripetizione, che aumenta la produttività e la qualità dei tovaglioli prodotti. I SeGMo forniscono inoltre dati importanti sullo stato dell’unità di piegatura e formazione dei pacchetti. La digitalizzazione della linea TV840 ottimizza l’efficienza della macchina apportando una maggiore sicurezza di processo.
Non solo sistemi interconnessi per Industria 4.0
La collaborazione transnazionale tra le due aziende prosegue, in quanto OMET prevede di espandere ulteriormente la propria tecnologia macchine in direzione di Industria 4.0. Anche Lenord + Bauer amplierà la sua gamma prodotti in quest’area, ad esempio con un software che consenta l’accesso remoto agli attuatori. A Oberhausen al momento si stanno effettuando test intensivi sulle possibilità del Condition Monitoring attraverso la manutenzione a distanza. La comunicazione in tempo reale e lo scambio di dati tra sottosistemi è solo un passo verso la completa digitalizzazione. Informazioni sullo stato di macchine e relativi componenti giocano un ruolo importante per l’intero processo di produzione. I dati aggiuntivi che il sistema di posizionamento può fornire, ad esempio per ottimizzare gli intervalli di manutenzione della linea del tissue, sono attualmente in esame. L’esempio mostra che Industria 4.0 non significa solo interconnessione di componenti e sistemi, ma richiede anche la cooperazione inter-istituzionale tra gestori, produttori di macchine e fornitori di sistemi.
Autore: Dr. Peter Velling, Head of Business Unit Machinery
Chi è OMET
OMET è un gruppo di aziende italiano che produce macchine per la stampa di etichette e imballi nonché per il tissue converting. Dalla fondazione avvenuta nell’anno 1963, OMET ha realizzato con successo in tutto il mondo oltre 1700 progetti. L’unità operativa delle macchine per il tissue converting ha sede a Lecco, Italia. Il portafoglio prodotti comprende 5 linee di macchine principali per la produzione automatica di tovaglioli usa e getta, asciugamani di carta, articoli in tessuto non tessuto e tovagliette.
Chi è Lenord, Bauer & Co. GmbH
Lenord, Bauer & Co. GmbH è uno specialista attivo a livello internazionale nel campo dei sensori di movimento e tecnologia di azionamento integrata. Nei settori Mobility e Machinery sviluppa, produce e commercializza soluzioni tecnologicamente all’avanguardia. Trasporto ferroviario nonché macchine utensili e d’imballaggio costituiscono i punti focali. Da oltre 50 anni, i clienti si avvantaggiano dei servizi di consulenza tecnica d’alto livello e dell’expertise nell’ambito delle applicazioni specifiche. Lenord + Bauer è certificata DIN EN ISO 9001, 14001 nonché IRIS.